This lift-type Industrial Debinding and Sintering Furnace for Ceramic is mainly used for debinding and sintering, wafer annealing, etc. It can also be used for high-temperature sintering and annealing of common metals or other materials. Maximum temperature 1750℃, ceramic fiber furnace chamber, touch screen control, lift type just needs a small area with large loading capacity. Bogie hearth design, easy to put and take the material. Low cost, high overall production efficiency, convenient operation, loved by domestic and overseas customers.
Applicable Materials: Si₃N₄ (nitridation of silicon powder), AlN (nitridation of aluminum powder), High-purity alumina (Al₂O₃) substrates, Silicon carbide (SiC) ceramics, Zirconia ceramics (Y-TZP), etc.
It can also be used for powder metallurgy, Metal Injection Molding (MIM), and the sintering of high-temperature alloys. Additionally, it can be employed in the preparation of cathode materials for lithium iron phosphate batteries (LiFePO₄).
Industrial Ceramic Debinding and Sintering Furnace Features
Smart Temperature Control & Exhaust Management
- Integrated air preheating (up to 400°C) exhaust system with gas filters and thermocouples for accelerated catalytic debinding.
- Four-sided heating with excellent uniformity.
- Automatic airflow control for efficient emissions removal.
- Top-chimney exhaust structure enhances gas flow dynamics.
Energy-Efficient Construction
- Multi-layer refractory materials:
– Hollow-sphere alumina (acid/alkali/molten metal corrosion-resistant, lightweight).
– Interlocking hearth structure (30% thermal stress reduction, improved thermal shock resistance).
– Mullite furnace base (50% enhanced load-bearing capacity). - Ceramic fiber-lined exhaust ports (erosion-resistant, zero slagging).
Full-Process Automation
- 10-inch intelligent panel with 30 programmable process curves.
- Three-phase asynchronous motor + worm gear lifting system:
– Linear guides + self-locking mechanism (±0.5mm synchronization accuracy, anti-drop protection).
– Programmable automated lifting sequences. - Automatic loading cart with dual safety limit switches.
Air-Cooled Debinding
- The variable-frequency fan system reduces energy consumption by 25%.
- Gas convection accelerates heat transfer, shortening debinding time by 30-50%.
- Minimizes carbon residues, pores, cracks, and impurities from binder decomposition.
- Lower energy consumption with improved yield rate.
Safety Protection
- Dual protection: Over-temperature/thermocouple failure auto power cutoff.
- Thermocouple break alarm with audible/visual alerts and emergency shutdown.
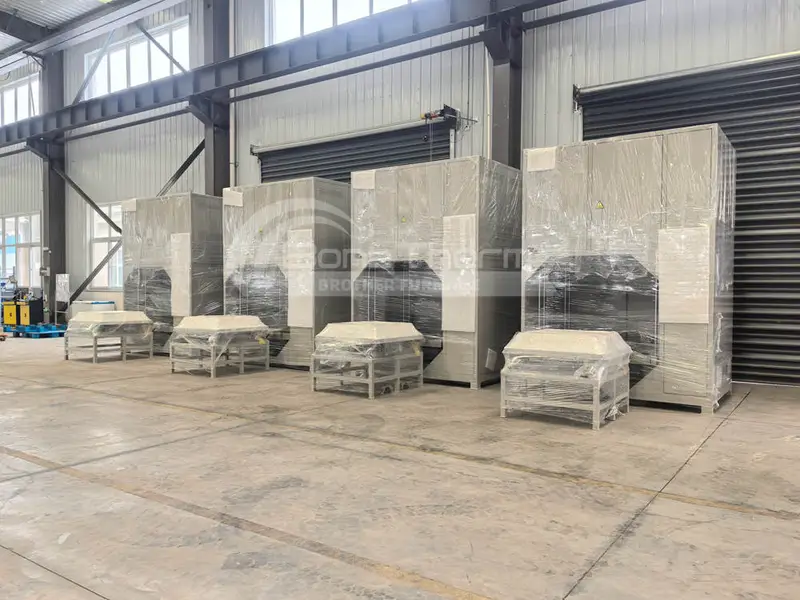
Applications
- Capacitor Ceramics
- Piezoelectric Ceramics
- Ceramic Cutting Tools
- Ceramic Bearings
- Artificial Bone (Bioceramics)
- Dental Ceramics
Ceramic debinding and sintering furnace standard size
Model | Max.Temp (℃) | Chabmer size (WxHxD in mm) | Liter (L) | Power (KW) | Phase | Heater | Thermo couple |
BR-17BL-8 | 1750 | 200*200*200 | 8 | 5 | 1 | Mosi2 heating elements | B type |
BR-17BL-12 | 200*200*300 | 12 | 7 | 1 | |||
BR-17BL-27 | 300*300*300 | 27 | 9 | 1 | |||
BR-17BL-36 | 300*300*400 | 36 | 11 | 3 | |||
BR-17BL-64 | 400*400*400 | 64 | 18 | 3 | |||
BR-17BL-125 | 500*500*500 | 125 | 40 | 3 |
Note: Other sizes can be customized.